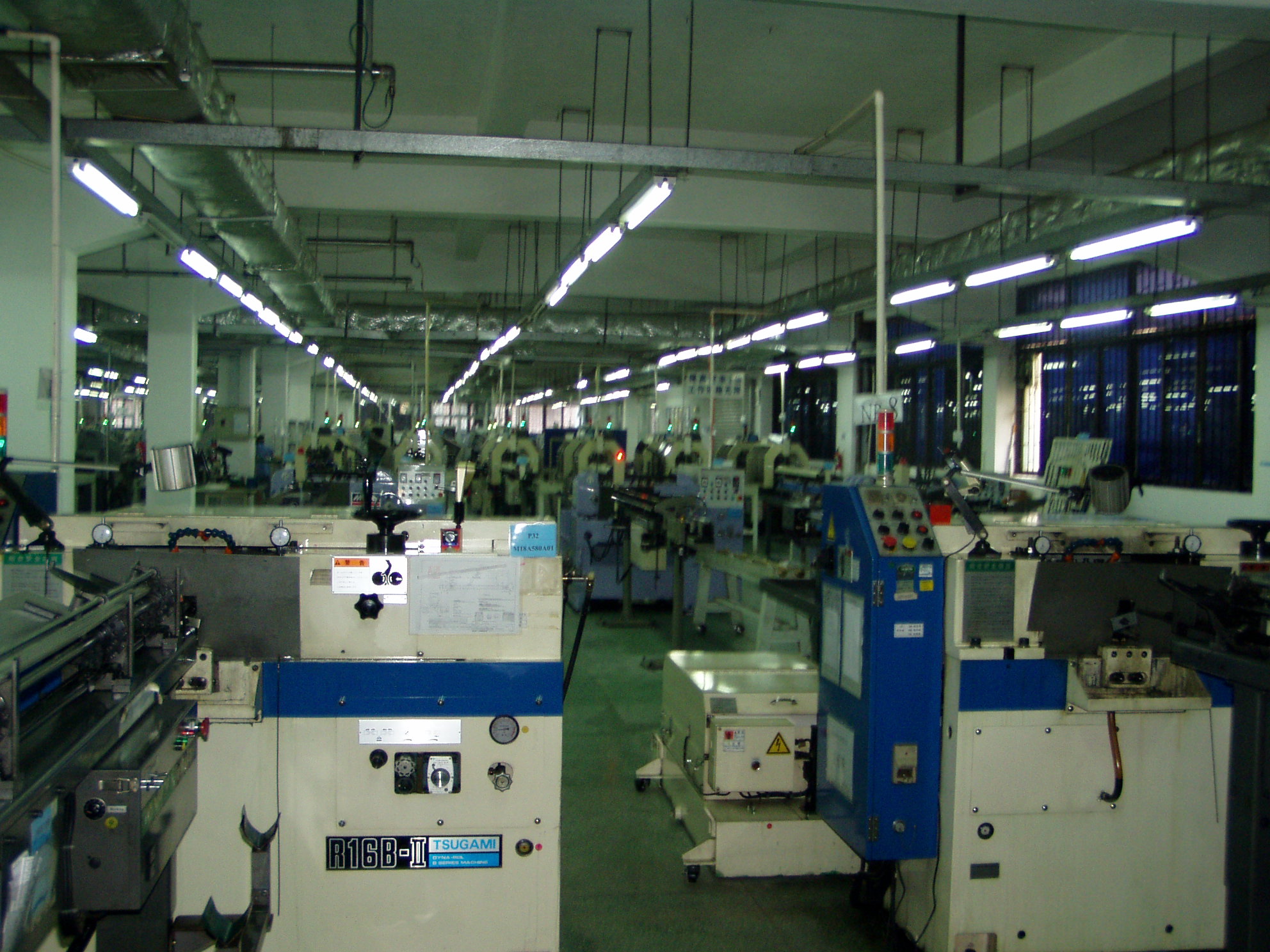
精细决定成败—精细化管理的日本企业
在日资企业工作了整十年,收获是很多,感悟也很多。感受最深的还是这里的精细化管理
下面是这家企业发展中的方方面面的精细化管理细节:
可能有人会认为精细化管理就是减少人员,减少支出等节约费用的一些行动吧,其实不然,精细化管理博大精深,是要通过全员的智慧,无数的努力和改善,利用最低的成本,创造最大绩效的一种管理模式。因为这涉及的面很广,只能摘取一部分来记录,或许有些参考价值。
1, 利用空间:
为了利用空间,车间的设备一年要搬动至少五次以上,有时只是为减少人员走动的距离,也要移动,以我所在的车间为例,二百多台设备,全部都是一二吨以上的大家伙,要移动是很困难的,而且要多个部门的协作才能完成。十年前这车间只有三十几台设备,增加到现在的二百五十多台,面积只增加了原来的一半,产量却增加了十倍以上,在这里的产量是以每平方米来计算的,产值也是以平方米计算的。虽然增加了这么的设备,但车间的设备却非常整齐,甚至还专门设置有供客户参观用的通道。其实不光是我们车间,整个公司也是这样做的,2000年公司的产量只有200多万台/M,现在有1400万/M,是原来的7倍,没有修建新的楼房,其实公司还有许多空地,也非常有钱,要建也是非常容易。最大限度利用空间在日本企业是普遍推行的,但在国内的企业,只怕是很少有去计算的。据说利用了空间,连照明电、空调用的电也节约不少。
2,挖掘设备潜能:
在这里,几乎所有的设备都被改造过:有的因为体积大占用空间多被改造;有的因为不太适合工法被改头换面;有的因为有的部件没有作用,浪费电被拆除;有的是为了只提高加工速度而更换高速马达;有的是为了提高材料的利用率而把设备锯短;有的为了提高供料速度更换部件的,有时并且不惜成本去改;为了提高设备加工速度,电脑加工程序需要经常被修改;有时为了改善品质,要增加各式各样的感应器的也有;为了提高产量,减少一秒的加工时间都要花很大的功夫去改善;每台设备的加工时间,每月都要进行测量并记录,总之尽最大可能挖掘设备潜能,所有的设备都这样高效率的运行着,产量提升了,投资成本,加工成本自然就降下来了。
3,节约一切物料,水电等资源:
为了节约支出,节约物料等资源,什么招数都会使用:
◆报价时一般选择三家以上的供应商报价,报价以后再有3至5次的降价要求,为了降价有时总经理都会出面交涉。
◆为了减少成本,有时会安排自己的技术人员去帮助供应商改善工艺,降低供应商的生产成本,然后根据供应商降低的成本,提出降低部品价格要求,这点是非常难能可贵的,不知在中国的制造业有无先例?(当然只指针对一些品质好,但不肯降价的供应商)
◆有专门技术人员针对一些废料,不良料进行分析,提出如何再利用等研究课题;一些治工具的回收利用率也非常之高。
◆物料的购入数量,使用量也控制得非常严格,所有物料都要进行预算,计划,盘点;FCOST(失败成本)管理 植入到每个人的意识当中。
◆为了节约成本,包装物料是必须回收的,并且要求回收率在90%以上(这当然需要与客户达成一定的回收协议);还有塑料周转箱使用率非常普遍,纸箱在车间内是被当作垃圾禁止使用的。
◆比较新的管理方式是预托品管理:供应商的物料放在自己的仓库内,没有使用之前,算作供应商的东西,不支付费用,只有在使用后,才支付费用给供应商。(一般比较有实力的公司才使用)
◆水电管理得很严格,每个部门的都有独立的水电表,每周进行统计,通报,有异常时要进行分析,处置,对策。为了节约水电:水流量控制在一定的范围内;在规定的温度的范围内才可使用空调;厕所、通道等全部使用5至10瓦的节能灯,车间的日光灯管数量也控制在合适的亮度内……
◆各部门的各种费用管理也非常严谨,基本上要做到所有费用都在预算之中,超出预算,有时要写对策报告的,这样报告特难写。日本人不只在公司是这样管理费用,连一般的聚餐都要预算,并且非常准确,有时连每个人的席位都会安排好。
4、 注重教育:
◆如何打招呼,如何行礼,如何接打电话等基本的礼议入社前都要教育,并且非常细致,资料也做得图文并茂。
◆最重要的是3Q6S教育,作为企业文化在推行,带动公司与员工进步。
5、全公司积极推行源流改善、三日间改善;重视问题意识、品质意识,成本意识、安全意识,改善意识。
精细化管理最终目的:品质最好,成本最小,利益最大。
经历了2008年世界性的经融危机的本企业不但没有停滞不前,产量还突飞猛进,提高将近一倍,显示了精细化管理在企业管理中重要作用。
(以上介绍的只是这家企业精细化管理的冰山一角,本人收集到该企业有数以万计的相关资料,可供参考)
免责声明: 本文内容来源于大平平 ,不代表本平台的观点和立场。
版权声明:本文内容由注册用户自发贡献,版权归原作者所有,武冈人网仅提供信息存储服务,不拥有其著作权,亦不承担相应法律责任。如果您发现本站中有涉嫌抄袭的内容,请通过邮箱(admin@4305.cn)进行举报,一经查实,本站将立刻删除涉嫌侵权内容。